Als 1977 bei Okulen in Ottenstein die Produktion beginnt, haben die fünf Gründer genau ein Produkt im Angebot: Skibeläge. Aus großen, runden Kunststoffscheiben, sogenannten Ronden, fertigen Bernd Huning, Norbert Krumme, Franz Schwanekamp, Hubert Schwanekamp und Engelbert Wassing die Beläge für die Bretter.
Und auch heute, über 46 Jahre später, laufen noch immer kilometerweise Ski-Beläge aus der Produktion. „Das macht aber heute nur noch zehn Prozent des ganzen Geschäfts aus“, sagt Rainer Gosling. Der 52-jährige Ottensteiner ist ein echtes Eigengewächs des Unternehmens. Nach der Ausbildung bei Okulen zum Industriekaufmann kletterte er die Leiter nach oben. Seit 2008 steht er als Geschäftsführer an der Spitze des Unternehmens, das immer noch im Besitz der fünf Gründerfamilien ist.
Der Betrieb mit seinen 225 Mitarbeitern ruht auf fünf Säulen: Die kleinste und älteste sind die Skibeläge. „Es gibt weltweit drei Unternehmen, die diese Beläge herstellen. Wir haben den kleinsten Anteil. Den halten wir aber stabil“, sagt Rainer Gosling.
Rund 30 Prozent des Umsatzes stammen aus der Produktion von Plattenware. Für die Kunststoffplatten werden pro Jahr rund 8500 Tonnen Polyethylen in den großen Pressen verarbeitet. Mal in große Blöcke, mal in Profile, um damit Baustraßen auszulegen und zu befestigen. Mal auch in Platten, um daraus Kunsteisbahnen oder Bahnen zum Eisstockschießen oder Curling zu bauen.
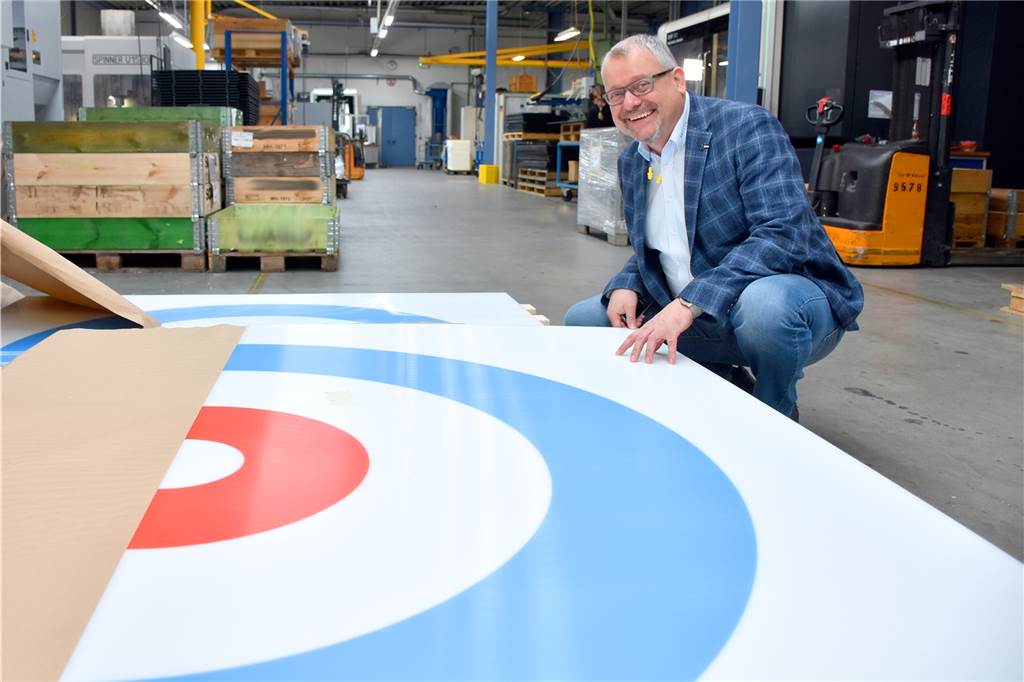
Andere Blöcke werden als Halbzeuge in alle Welt exportiert. Gut die Hälfte der Produktion wird direkt verkauft. Davon wiederum ein Großteil nach Asien oder sogar Australien. Zerspante und verarbeitete Teile bleiben in Deutschland und Europa. Auch in die andere Richtung ist Okulen weltweit tätig: Rohstoffe werden aus ganz Europa, Asien und den USA nach Ottenstein importiert.
Das Hauptgeschäft von Okulen ist längst die Zerspanung und Profilbearbeitung großer Kunststoffelemente – gut 40 Prozent des Umsatzes. „Alles was man drehen und fräsen kann, stellen wir her“, sagt er. Mit modernen Drei- oder Fünf-Achs-Maschinen, von wenigen Millimetern bis zu acht mal zwei Meter großen Teilen. Profilleisten können sogar in bis zu 16 Metern Länge bearbeitet werden.
Entsprechend riesig sind die Anwendungsbereiche: Fördertechnik, Maschinenbau, Lebensmittelindustrie bis hin zu exotischen Feldern wie Fendern im Hafenbau.
Formpressen und LKW-Anhänger
Das nächste Feld ist das Formpressen: Etwa Bauteile von Pumpen werden nicht aus einem Kunststoffblock herausgefräst sondern direkt in Form gesintert. Ein Verfahren, bei dem aus dem Kunststoffgranulat unter hohem Druck und Temperaturen knapp unter dem Schmelzpunkt das Werkstück entsteht.
Wieder ein völlig anderes Geschäftsfeld eröffnet sich in der letzten Halle auf dem Gelände: die Auskleidung von großen Muldenkippern. Die großen Mulden werden bei Okulen mit speziellen Kunststoffplatten ausgekleidet. Dadurch werden sie beispielsweise haltbarer als die herkömmlichen Alumulden. Oder die Ladung gerät auf den Kunststoffflächen schneller ins Rutschen. „Wenn man auf der Baustelle deswegen die Mulde nur ein paar Grad weniger kippen muss, kann das schon den entscheidenden Unterschied ausmachen“, sagt Rainer Gosling.
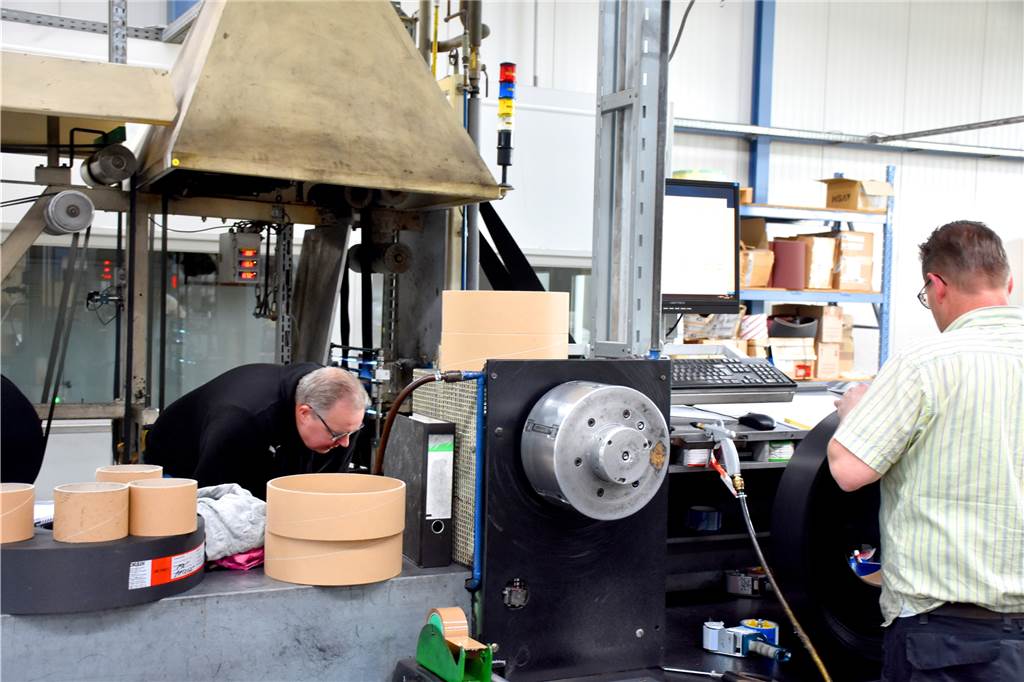
Diese weite Verzweigung macht das Unternehmen extrem robust: „Keiner unserer Kunden hat bei uns mehr als zehn Prozent Anteil am Umsatz“, sagt Rainer Gosling. Auch deswegen sei das Unternehmen bisher durch alle Krisen gekommen. Selbst die Unwägbarkeiten auf dem Energiemarkt Ende 2022 sind schon wieder vergessen: Die Energiepreisbremse funktioniere. Die Nachfrage sei da. Die Auftragsbücher sind auf Monate im Voraus gefüllt.
Rainer Gosling führt Besucher gern durch die Hallen im Gewerbegebiet Im Garbrock. Nur zu sehr ins Detail darf er nicht gehen, selbst wenn er gerne würde. Es gibt eben doch ein paar Geheimnisse. „Und wenn ich die verrate, bekomme ich Probleme mit unseren Technikern“, sagt er lachend. Das wolle er nicht riskieren.
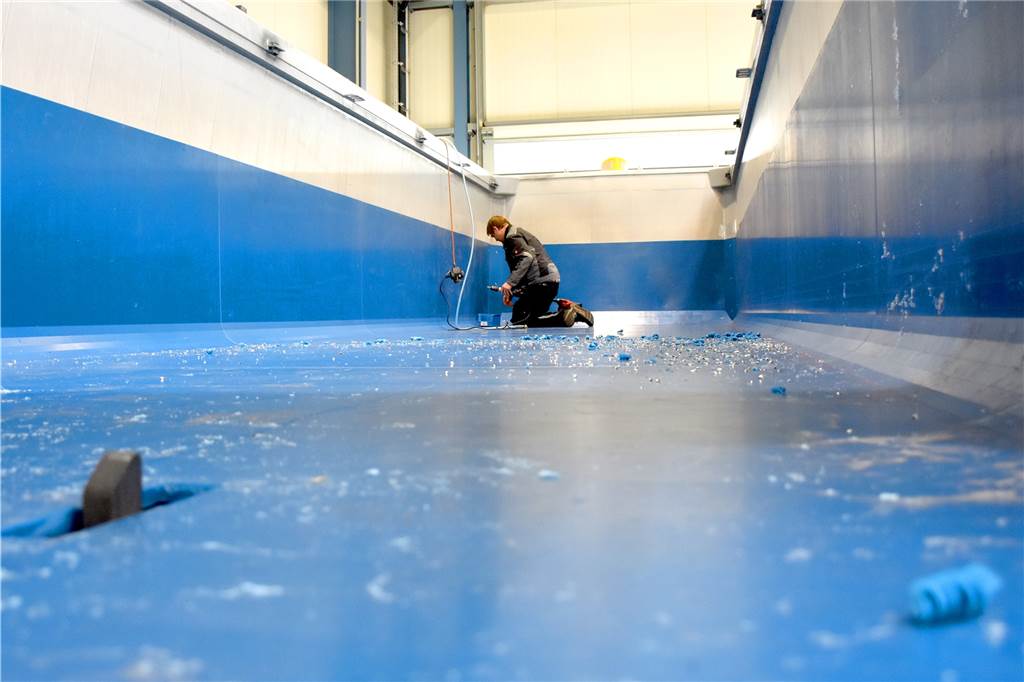
Denn natürlich seien auch bei Okulen die Menschen das eigentliche Kapital. Seit Gründung des Unternehmens bildet das Ottensteiner Unternehmen aus. Industriemechaniker und -kaufleute, Elektroniker, Zerspanungsmechaniker – ständig sind 10 bis 15 Auszubildende beschäftigt.
„Aber die Fülle der Bewerbungen ist weniger geworden“, sagt Rainer Gosling. Trotz vieler Quereinsteiger fehle der Nachwuchs. Die Angestellten blieben dem Unternehmen zwar über Jahrzehnte treu, das Betriebsklima sei sehr gut, aber nach 45 Jahren Unternehmensgeschichte müsse man jetzt ja auch die ersten Verrentungen verkraften.
Automatisierung ist ein Schritt
Weitere Automatisierung sei da ein Schritt, um dem Fachkräftemangel vorzubeugen. Gleichzeitig sollen die Jobs so attraktiv wie möglich sein. Dennoch: Beispielsweise ganz ohne Wochenendarbeit gehe es nicht. Doch seit rund zehn Jahren seien beispielsweise die Schichten am Samstag immer schwieriger zu vermitteln. „Da fehlt der Feiertagszuschlag“, sagt Rainer Gosling. Noch setze das Unternehmen auf Freiwilligkeit.
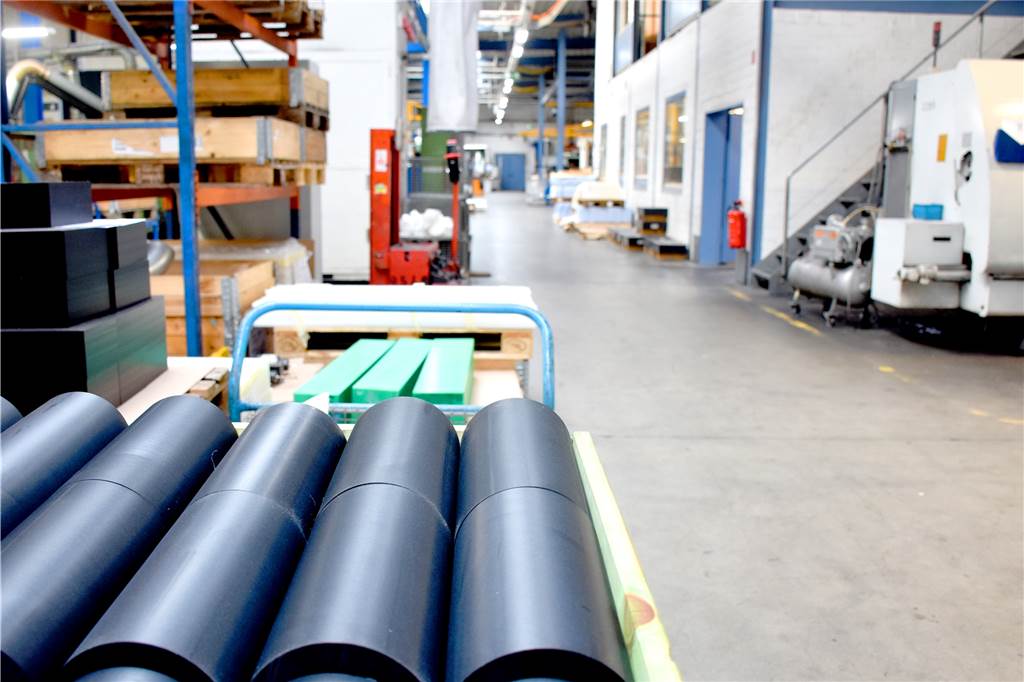
Was die Zukunft angeht, sei die Personaldecke noch zu halten. Auch durch Prozessoptimierung lasse sich noch einiges erreichen. Und ja, auch der Ausbau einiger Kapazitäten sei noch geplant. Eine neue Halle etwa sei in Planung. Weitere fünf bis sieben Millionen Euro könnten bis zum 50-jährigen Bestehen der Firma in einigen Jahren noch in den Maschinenpark fließen.
Wachstum ja, aber nur organisch. Das bleibt das oberste Gebot.
Dieser Artikel erschien zuerst am 1. Februar 2023.
Rauschendes Fest auf dem Tobit.Campus: Hans-Georg Althoff feiert Abschied von Ahaus
Corona-Isolation fällt weg: Ahauser Arbeitgeber müssen mit schwieriger Situation klarkommen
Kein Restaurant mehr: Pietsch nutzt ehemaliges Mona Lisa in Zukunft nur für Mitarbeiter